The Role of CAE in Medical Device Development
Understanding the role of simulation in the development of medical devices.
The medical industry is one of the most complex and regulated sectors of the economy—and for good reason. Medical devices offer an opportunity to drastically improve the health and quality of living for millions of patients each year, yet the risks of a faulty device are equally great. The devices that might save a patient could also prove fatal, or cause other lasting injury, if the design behind them is poorly developed.
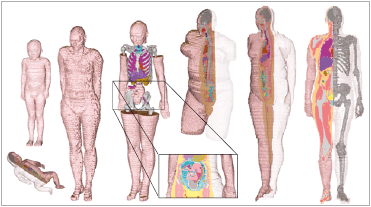
Complete set of CST Studio Suite Voxel Family models,
showing the range of ages and body shapes available.
This places the developers and manufacturers of medical devices in a difficult situation. Whereas many other fields can innovate in relative freedom, medical manufacturers must be able to demonstrate their designs are substantially equivalent to predicate devices or that the benefits outweigh the residual risks. Accordingly, manufacturers in the healthcare field face a high burden of proof before they are allowed to market their devices. For devices so novel that there is no predicate device to compare, sometimes a clinical trial is required, which is costly and may take many years.
In recent years, the FDA has recognized the advantages that CAE (Computer Aided Engineering) simulation brings to this design and development process. Simulation provides a fast and inexpensive way to demonstrate proof of concept for a new device and to mitigate associated risks. To guide manufacturers in their use of CAE, a guidance document providing procedures to standardize verification and validation of computational modeling of medical devices (ASME V&V 40) has been developed and recognized by the FDA. This guidance provides a framework for assessing the relevance and adequacy of completed V&V activities that establish credibility of a computational model associated with a medical device.
Class I: External devices that pose low risk to the patient
The first class of medical devices encompasses a wide range of external devices that are considered low risk because they are not intended for use in supporting or sustaining life or of substantial importance in preventing impairment to human health. Class I devices represent 47% of all medical devices. Examples of devices that are considered Class I are tongue depressors, bandages, crutches, dental floss, etc. Class I devices do not require FDA clearance or approval, but simulation can improve their design and effectiveness.
Class II: Moderate to high risk to the patient
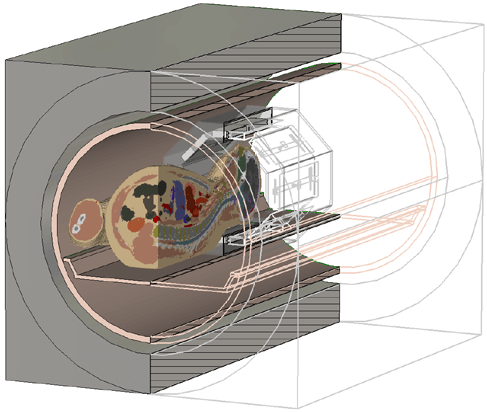
A model to test an 8 channel head coil, including the magnet bore,
the gradient coils and the HUGO voxel model.
Class II devices make up 43% of all medical devices and are considered higher risk devices than Class I. These may include those which enter the body or are implanted in the body in some way, such as catheters or orthopedic implants. These devices therefore require Premarket Notification (510(k)) for FDA clearance. The 510(K) is a streamlined regulatory clearance process using a predicate device to prove the new device is substantially equivalent using physical testing and CAE. The device can then bypass the clinical trial or PMA Approval process and receive clearance from the FDA. This greatly reduces the time-to-market for much-needed devices.
Example: COMBINED 3D ELECTROMAGNETIC AND SPIN RESPONSE SIMULATION OF MRI SYSTEMS
Modern MRI systems are very complex and it is important during the design phase to understand the interaction between the body and the device while it is in use. This analysis helps designers understand how energy is absorbed by the body so it can mitigate the possibility of harmful heating.
Class III: High risk life-supporting or life-sustaining devices
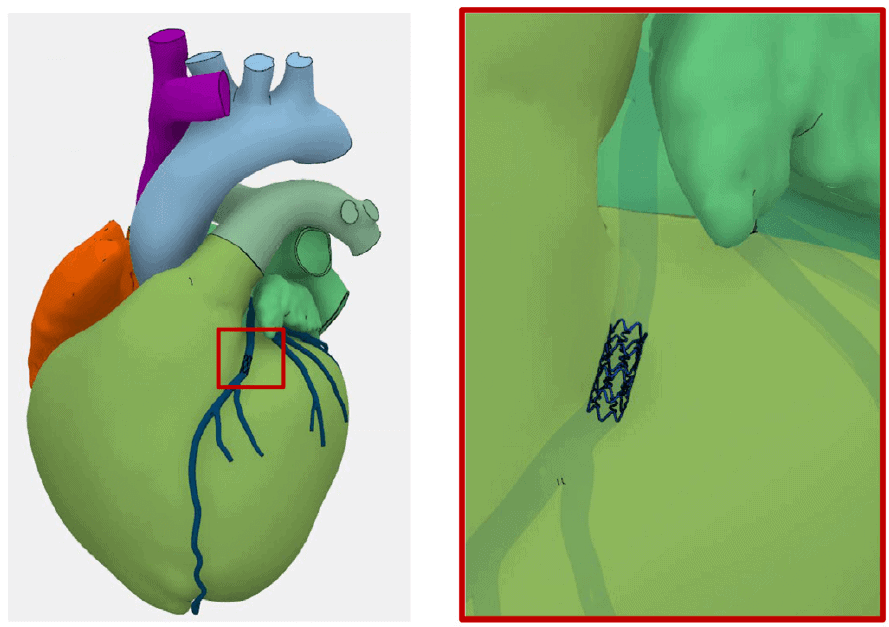
Coronary arteries (blue) and stent added to the SIMULIA Living Heart Human Model. Zoomed-in view shows the stent aligned with the coronary arteries.
The final class of devices making up 10% of the market are those which pose significant risk to the patient as they are considered life-supporting or life-sustaining. These devices go through the Premarket Approval (PMA) process to obtain FDA Approval. This is the most involved regulatory process, especially if there is not a predicate device that could be determined to be substantially equivalent.
Like a Class II device, CAE can be utilized to help prove substantial equivalence in addition to physical testing. If there is no substantially equivalent device, CAE can also be used to help understand the severity of risk factors as well as determine what device configurations need to undergo physical testing as a worst case, thus minimizing the amount of physical testing needed. Examples would include stents, pacemakers, and left ventricular assist devices, all of which are difficult to remove after implanted, and are used to sustain life.
Example: LIVING HEART HUMAN MODEL: CARDIOVASCULAR STENT DEPLOYMENT AND CARDIAC CYCLE SIMULATION
Cardiovascular stents are critical devices to restore the function of blocked or narrowed cardiac vessels. When designing and developing a stent, it is of great importance to understand the durability of this small metallic device, as it is both permanently implanted and life-supporting. The SIMULIA Living Heart Human Model provides a unique testing environment where a stent can be deployed and mechanically studied.
5 ways CAE simulation helps healthcare developers improve their medical devices.
CAE can be used for every class of medical device, and can provide benefits to developers whether or not clearance or approval is required for the device. Here are five ways simulation can benefit medical device developers.
1. Optimizing product design in the development phase.
At any classification level, CAE simulation can improve devices by helping engineers adjust design variables to determine how a design change might affect device performance in the R&D phase. For instance, a metallic stent design could be modeled with different geometric sizes of laser cut slots to ensure sufficient radial force is being applied to the arterial wall.
2. Testing designs of a new device before it moves to a bench study.
Bench studies allow developers to subject a device to various tests to see how it performs under loading conditions. If there is a design flaw at this stage, the bench study can identify it before it goes into the production or regulatory process.
However, physical bench tests often are costly and time consuming. A simulation of the physical test can provide confidence that the device will pass before the test pieces are even produced. Simulation can also be used to determine what configuration of the product family would be considered worst case, thus further reducing the amount of testing required.
3. Demonstrating equivalency to a predicate device.
CAE simulation can be used to help demonstrate equivalency by comparing a new design against a predicate device. This is especially convenient for product line extensions, where there is concern that a new design or modification presents a new worst case. This data can be used to help with the regulatory submissions to prove substantial equivalence.
4. Simulating extreme scenarios that would be difficult or unethical to perform.
Devices interact with the human body in numerous ways, and next generation device ideas often push the limits of existing devices in the market to improve patient outcomes. To understand the effectiveness of a proposed design, simulation can often be the only solution. For example, in the example stated above, a novel MRI system would be unable to test this device on a living human. Simulation would be the tool of choice to understand the energy absorption/heat generation in a human body model.
5. Simulating testing failure or in-field failure to determine root cause.
When a required test failure or in-field failure occurs, it is very important to quickly understand what is the root cause that generated the event. Simulation can provide fast insight to recreate a scenario to understand the anomaly and help drive decision making for appropriate stakeholders.
CATI can supply the CAE needed to bring medical devices to market.
Over the years, CATI has provided CAE for numerous devices in the healthcare industry. Beyond this, we have numerous CAE specialists on our team who have attained PhDs and Master’s in biomedical engineering, and whose knowledge of the medical engineering field is at the top of their profession. If you need CAE simulations at any stage or your device’s lifecycle, we can provide them. Contact us to learn more about how we can work with your team.