3D Scanner Basics
What are 3D scanners?
Simply put, 3D scanners are devices that are used to take real-world, tangible objects and transfer their geometry into computer data. They provide an alternative measurement method to options such as hand measurements that are slow and unreliable or using a CMM (coordinate-measuring machine) which are slow and require you to move your part to a lab and place it in a special fixture.
Our 3D scanners don’t require any hard setup of the part nor the part to be moved to a metrology lab in order to get extremely accurate measurements that anyone can achieve. In addition to that, instead of getting just a few key measurement points, 3D scanners will gather millions of measurements for you so you can easily get the whole picture of what you’re measuring. This means that if you’re just measuring a few points on the part or 100 it takes almost the exact same amount of time. The flexibility, speed, accuracy, repeatability, and ease of use are what set 3D scanners apart from other measurement methods.
How do 3D Scanners Work?
The Creaform 3D scanners use a grid of laser lines or white light lines that, when reflected off the surface of an object, allow the scanners to create hundreds of thousands of distance measurements per second. (1.5 Million per second in the case of the Go!SCAN SPARK!)
But these are just distances. Using target stickers placed on or around the object being scanned lets the scanner create a reference frame so it knows where it is in space compared to those targets. A good reference frame allows the scanner to combine all the distance measurements and create a seamless scanned surface. This surface mesh can then be used in many ways such as comparing against existing 3D CAD (computer-aided design) models for quality assurance or being used as a reference for creating a new CAD model.
3D Scanner Limitations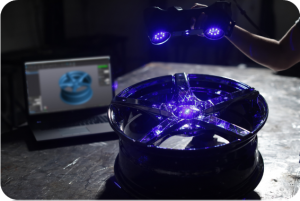
As optical devices, they can only measure what they can see. They have a fairly wide viewing window that’s over one square foot in size for the HandySCAN and Go!SCAN 3D scanners but they also have a distance window where they are most effective. They operate best when they’re about one foot away from the surface they are measuring. This means if you can’t get close enough to the item being scanned or there are too tight of geometry like the inside of a pipe you won’t be able to scan.
The surface finish of the part is the other main limiting factor to the speed and ease of scanning. Surfaces that are very shiny (polished chrome), black, or see-through make it hard for the scanners to pick up the lights they emit. However, in most cases, this can be remedied by very simple software changes like changing the shutter speed of the camera to let more/less light in. As you can see in the picture, the HandySCAN BLACK is still able to scan the surface of this polished chrome wheel!
Conclusion
I hope this brief introduction to 3D scanners was helpful and informative. They are extremely powerful tools that can help in many different workflows. If you want to know more about 3D scanners and if they could be right for you and your company, we suggest viewing some of the other blog posts on our website about them, watching some of the many Creaform videos on our YouTube channel, or getting in contact with one of our sales representatives who can start conversations with you and our engineers to find the best fit for you.
If interested, here is a link to our 3D scanning solutions page on the CATI website.
Nathan Fears
Application Engineer – 3D Scanners & SOLIDWORKS
Computer Aided Technology, LLC