How Integrating CAE into the R&D Workflow Saves Costs
Simulation can aid every stage of development, from exploring concepts, to validating designs, to guiding redevelopment.
They say that necessity is the mother of invention, and in the business world, necessity usually means competition. Product developers in every industry face tremendous pressure to create new solutions to old problems—or new solutions to the new problems created by the last round of solutions. It’s a constant cycle of innovation and refinement, and only those organizations committed to improvement stay viable.
However, in an industry defined by innovation, the biggest innovation may be the one redefining the research and development process itself. Computer Aided Engineering has been around for decades, of course, but as the technology has advanced, it has become more powerful—and more applicable to a wider range of scenarios. It has also become more affordable, so that more companies are able to access it and include it in their design process than ever before.
The biggest question facing these companies is: how? If the old development cycle was “build, test, redesign,” where does simulation fit in? The answer is: everywhere. Let’s take a look.
I. Development research: CAE enables more experimental concepts.
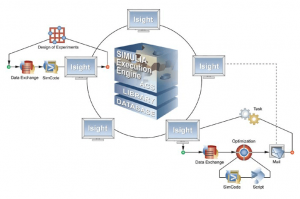
An automated analysis cycle for design iterations
One of the most difficult things to determine in a design cycle is which ideas are worth pursuing. The more radical a design change is, the more risk there is in developing and prototyping it, because it is more likely to fail. But the more a design follows the assumptions of preceding designs, the less likely it is to be truly revolutionary.
CAE simulation can resolve this conflict by providing proof of concept at early stages of a developmental design. Effectively, it allows engineers to take greater leaps in their designs without increasing the risks to the company that those designs will fall flat.
II. Product testing: CAE can validate a design before the prototyping stage.
Once a design has been developed, it moves into the testing stage. Testing has traditionally been conducted using prototypes—either of individual components, or of fully assembled end products. Unfortunately, prototype development can be costly, especially if testing involves damaging or destroying the prototype to determine how well it handles wear and tear.
CAE simulation can validate designs before they go into the prototyping stage, increasing the confidence in the success of a certain design, and in some cases, reducing or eliminating the need for certain tests. Simulations can also offer new tests for scenarios that would be too difficult to test for (plane crashes, for instance), or in situations where testing would be unethical (as in products designed for use within the human body).
III. Redevelopment: CAE can guide developers toward more cost-effective designs.
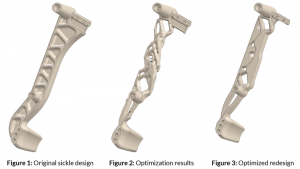
Design optimization for strength and lightweighting
Finally, for products that fail the prototyping and testing stage, CAE simulation can offer insight into why the design failed, and into modifications that would improve its effectiveness. By guiding engineers toward design solutions, simulation reduces the turnaround time and helps businesses return to the testing stage faster.
4 ways CAE leads to a more cost-effective R&D workflow:
Now that it’s clear how you can include CAE in your R&D process, you may be wondering if it is worth the effort. Many organizations have spent decades honing their development process to be as efficient as possible. Will it really be cost effective to rework that system to include an entirely new process?
We believe the answer is “yes.” Here’s why.
1. Bad designs are eliminated earlier in the development cycle.
The further a design gets in the development cycle before being eliminated, the more costly it is to the company. If a simulation shows that a certain design won’t work, the only waste involved is the time used to create the design itself. But if a design gets all the way to the production stage before a design flaw or inefficiency is discovered, that waste includes the cost of the design, the costs of engineering and prototyping, and eventually the production costs as well. Early verification through simulation can save businesses millions in production waste.
2. The cost of expensive prototypes is reduced.
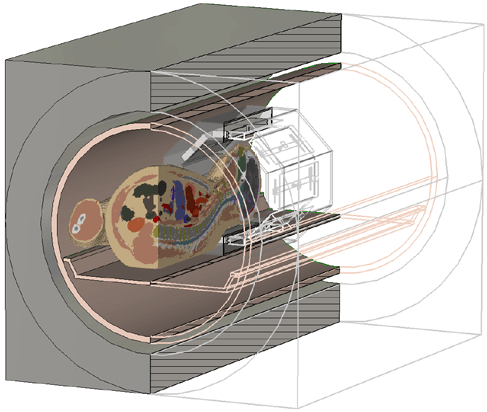
EM simulation of MRI machine on the human body
Simulations don’t just pre-validate designs before they go into prototyping. They can also save on the overall costs of prototyping by replacing some of the tests. In the design of an office chair, for instance, a simulation might run a hundred tests to show how the chair operated under various use conditions, at different reclining angles, and with people of different weights and sizes. A physical prototype would only need to replicate a handful of those simulations to demonstrate that the simulation model was accurate.
3. Shorter development cycles mean less product development time.
Eliminating bad designs early and shortening the prototyping phase means that new designs spend less time overall in product development. A shorter lag between concept to market means fewer resources spent on R&D.
4. All the above lead to greater market competition.
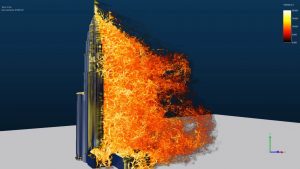
Architectural CFD simulation
Fewer sunk costs in failed product designs, reduced prototyping expenses, and a faster time to market all mean that businesses can be more responsive to shifting market trends, and can deliver their products at a lower price point than their competition. This in turn makes them more competitive on the market, without loss of any product quality.
Our team of CAE engineers can give your business the competitive edge it needs.
Many businesses want to integrate simulation into their R&D departments, but don’t have skilled engineers on staff. Others have an engineering team with CAE expertise, but can’t manage the workload. Fortunately, we’re here to help.
We have a team of CAE and FEA experts who can expand the simulation capabilities of your company. Whether you want a VAR to guide you through purchasing CAE simulation software for your engineering department, or CAE experts who can run simulations for your team, our engineers have the knowledge to support your project. Contact us today to get started.