Stratasys 3D Printing: 3D Printer or Rapid Prototyping Solution?
How to Spot the Difference (and Save Millions) – Part 1
Another Year. New Challenges for the Product Innovation Firm.
Before diving into your next 3D printing purchase for Rapid Prototyping (RP), let’s put your product development process in focus.
The product development process, which transforms a concept into a market-ready product, plays a critical role in both the functional and economic success of your product and parent company.
It is therefore crucial for firms to effectively mveasure the performance of their product development cycle – using factors including lead time (the calendar months/years that pass from concept development to the end of pilot production) and engineering effort (the person-months/years required to go from concept development to the end of pilot production).
Then consider that over the last few years consumer demand for product variety and customization has only increased. On top of that, consider that product lifetimes are constantly falling. To stay competitive, not only do you need to develop more and more products, but you need to be prepared for the fact that they stay in the marketplace for shorter and shorter windows.
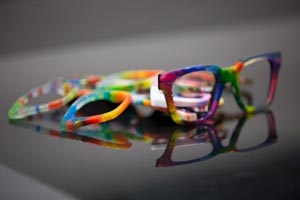
Designer frames prototyped with color and patterns on the Stratasys J750 full-color, multi-material 3D Printer.
This means your product development cycle must be smarter, more agile, more productive and more efficient. In addition, the decisions you make in the early stages of the product development cycle can ultimately affect multi-million dollar investments further down the path.
So what does this mean for you, the product design and development company, as we begin 2017?
Enter Rapid Prototyping
3D printing, the series of technologies allowing firms to rapidly turn on-screen designs into one-off physical objects, has been in use for nearly three decades by many of the world’s largest and most demanding design and manufacturing companies. Since the turn of the millennium, it has also rapidly filtered down to smaller enterprises, dedicated RP shops and design workgroups, to the point that most fully recognize the opportunities of 3D printing. Many see the technology as integral, even indispensable, to their design and product development cycle. But beware – not all 3D printing solutions are alike!
Myth: The Only Difference between General Purpose 3D Printers and Professional RP Solutions is Price
Over the past two or three years there has been an explosion in small, entry-level, general purpose 3D printers that claim to have ‘professional’ prototyping capabilities in their literature.
While such 3D printers are indeed a useful entry tool to the wider technology, a company looking to make a serious dent in their product development cycle must be aware of all the factors that separate professional RP from general 3D printing. Here are just a few questions worth asking before you take the plunge:
1.) How much of the RP workflow can this system actually handle?
It’s all very well talking about prototyping, but what does it involve exactly?
At the concept verification stage, you need a system that can churn out multiple simple iterations, fast, in a cost-effective model material. At this point in the RP process, you’re mainly evaluating ‘form,’ or what shape the product will take. And it’s here that a general entry-level 3D printer will perhaps perform best – as long as the model isn’t overly large or complex.
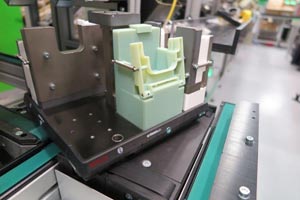
3D printed functional prototype being tested on the assembly line at Schneider Electric.
At the design validation stage, you’ve narrowed your design down to one or two finalists and now you want to test both ‘form’ and ‘fit,’ which, depending on your product, will demand high tolerances, multiple materials or colors in a single build, thin walls, complex geometries (requiring soluble support material), moving parts and more. For any serious design validation effort, the majority of small, desktop 3D printers will simply not provide the accuracy, detail and repeatability needed.
Finally, you want to test the design’s functional performance – using stress tests, drop-tests or limited real-application usage. For this stage, engineering-grade materials are key. If cost-effective PLA material was ideal at the concept stage, for functional performance you need production-grade ABS, ASA, PC, PC-ABS, various Nylon grades, ULTEM and more.
Looking beyond the relatively narrow focus of the RP workflow are larger questions relating to learning and operating time, support and future-ability. Questions such as:
2.) How much time do I have to invest getting it working, operating day to day, and in maintenance? And…
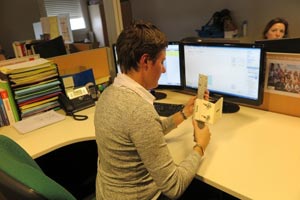
Evaluating a 3D printed part prototype at Sodimas Elevators.
3.) How scalable is it to my future needs?
Here again, the differences between the plethora of readily available 3D printers and professional RP systems can be stark. Most entry-level 3D printers are still new to the market and have generally undergone minimal rigorous field testing. They have little in the way of supporting workflow tools and, due to the limited scope of the supporting vendor, tend to have very little in the way of global customer support – all of which affects your overall RP efficiency and effectiveness for the medium- to long-term.
Conclusion: Think about Overall Solution Effectiveness
All this means that firms focused on building competitiveness must act fast to compress their product design and development cycles with a systematic approach to RP and 3D printing. This means weighing the pros and cons of general purpose entry-level 3D printers vs professional RP systems.
A good starting point is to consider the intellectual property, engineering and software investments that have gone into developing the overall effectiveness of the solutions available. Then consider how this affects both your lead time and engineering effort. You may be surprised to find the differences can add up to millions, if not billions, in costs over the development effort and the lifetime of your intended end-product.
Stay tuned for Part 2 to learn how to better quantify Overall Solution Effectiveness.