Designers, engineers, and manufacturers across multiple industries are discovering that the more ways they can incorporate 3D printing into a product’s developmental life cycle, the better they can optimize ideas, time management, and product developmental dollars. In the not so distant past, prototypes and concept models were made of wood, clay, or metal. They often had to be made in third party shops, where the time and costs associated with producing models was difficult to justify to management.
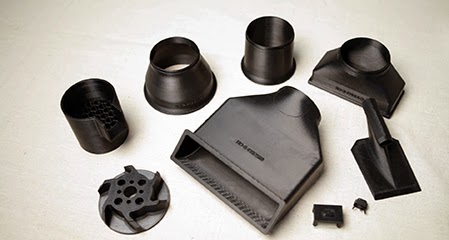
What 3D printing has brought to the table has been nothing short of a game changer for product development. In the early phases of product development, the ability to create multiple versions of a basic product design with subtle but noticeable variations allows designers the ability to determine the product’s best fit and feel possible. Performing clinical trials in-house, and quickly streamlining the process of moving from concept to functional testing, helps ensure that deadlines for manufacturing can be met.
3D printed models contribute to improved communication between design and manufacturing departments. The ability for a design department to produce working prototypes that can be held and manipulated by the manufacturing team helps bridge the gap between 3D CAD data and the final look of the product. Working prototypes enable a designer to identify and make needed adjustments to a design before handing it over to the manufacturers. The same applies for the manufacturing team who, based on the physical 3D model provided, may see problematic spots on a part that the design team could address. This is much more efficient than shipping the CAD data off and then finding the issues when the part goes to production.
Possibly the most overlooked aspect of the importance of 3D printing is using a functional prototype to quickly present to focus groups. How valuable is it for a company to be able to obtain detailed feedback from customers before taking a product to the manufacturing phase? The more quickly a company can process and apply customer feedback to the manufacturing process, the faster they can get a product to market.
The ability to save time and maximize every dollar spent in product development are the primary drivers for incorporating 3D printing. The ability to produce tools in-house that help speed up and optimize the decisions to move a product to the next phase of design gives companies an edge against their competition, and helps them better meet the demands of their customers.To learn more about 3D printers, check out our site by clicking here.