Why SIMULIA for SOLIDWORKS? 3D Experience Simulation and SPH Elements
There are many reasons businesses have been shifting to the cloud over the last few years; flexible licensing schemes, data backups & security, downsizing internal IT overhead, the list goes on. All sorts of industries are moving in that direction, and design verification and simulation are no exceptions. Cloud based simulation benefits from all the items listed above, and more. Today, I would like to cover a feature that differentiates SIMULIA for SOLIDWORKS on the 3D Experience Platform from SOLIDWORKS Simulation; that is the ability to include fluids in your FEA Structural Simulation.
In today’s simulation industry, FSI (Fluid Structure Interaction) is a big buzzword. It allows simulations of structures that deform due to fluid flow, which then changes the profile of the fluid flow, which then changes the deformation of the structure further, etc. This two-way interaction between FEA and CFD solvers can be incredibly complex and time consuming. Luckily, there are a couple of features built into SIMULIA for SOLIDWORKS that can ease this process: SPH Elements and Fluid Cavity domains. This Blog will focus on SPH Elements.
Smoothed Particle Hydrodynamic Elements, or SPH elements for short, are a way to model the effects of a fluid on a solid structure without coupling the structure with a CFD solver. In basic terms, this feature converts a solid part mesh to a lattice of rounded, smoothed, particles that represent a discrete volume of the fluid. Unlike traditional elements, these particles can move freely between each other and separate from each other. I like to think of it as describing a fluid like a ball pit that your kid’s might play in. The smaller the balls in the pit, the more the pit acts like a fluid.
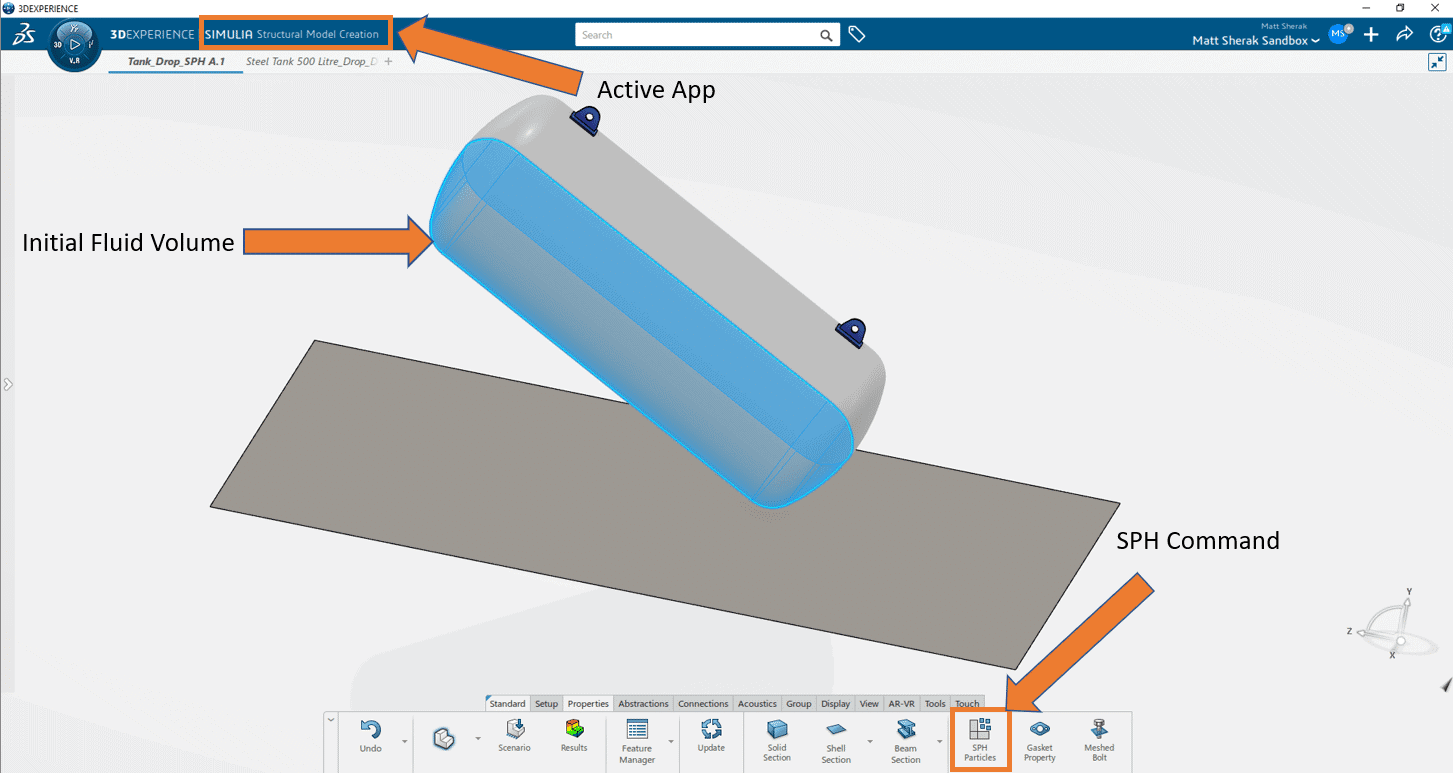
Figure 1
I’ll demonstrate SPH elements by simulating water sloshing around in a tank. In the figure above, you can see the highlighted solid body- representing the initial level of the fluid.
Adding SPH elements into your SIMULIA for SOLIDWORKS simulation study must be done through the structural model creation app. Select SPH from the Properties tab of the command manager, see figure 1.
NOTE that you must have a mesh created prior to converting to SPH elements and only reduced integration solid elements C3D8R, C3D6, and C3D4 can be converted to SPH particles.
Next, we will have to define the properties of the SPH particles.
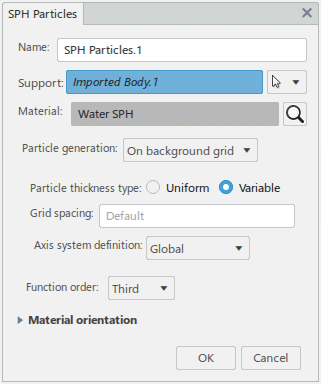
Figure 2
We can give the definition an optional name. From there we select the body that we wish to convert to SPH, assign a material, and determine the generation method. There are two options here:
- On background grid– This creates a background lattice in the model. The particles are then placed at the grid intersection points. You can then determine the grid spacing size and the order formulation of the SPH elements added (second, third or fifth order). See figure 2 above.
- Per element– See figure 3 below. This option converts the FEA mesh element directly into SPH particles. You can insert one to seven SPH particles per FEA element using the particles per isometric direction box. The SPH will be divided as seen below in figure 4. This definition also benefits from second, third or fifth order formulations.
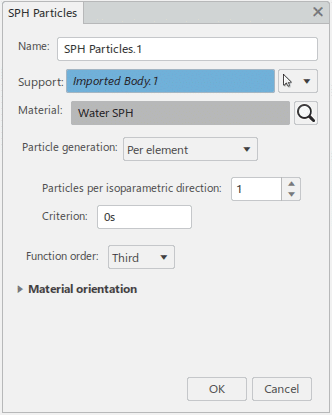
Figure 3
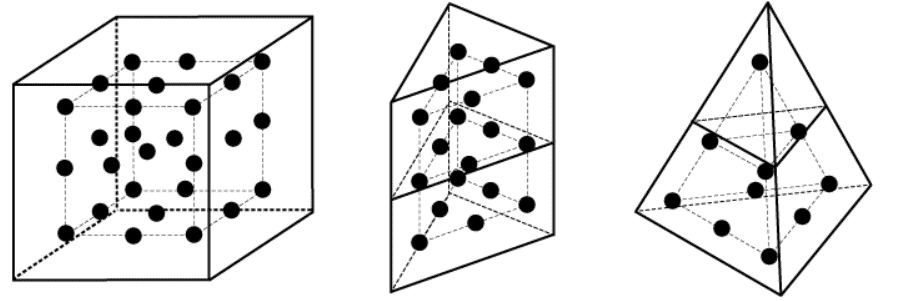
FIgure 4
(Image courtesy of Dassault Systèmes)
Finally, once the remainder of the fixtures, loads and contact definitions are complete we can run the study. For the example we are working with, I am going to follow the procedure for setting up a drop test using the explicit solver. You can find more information on drop test setup using the Structural Mechanics Engineer role.
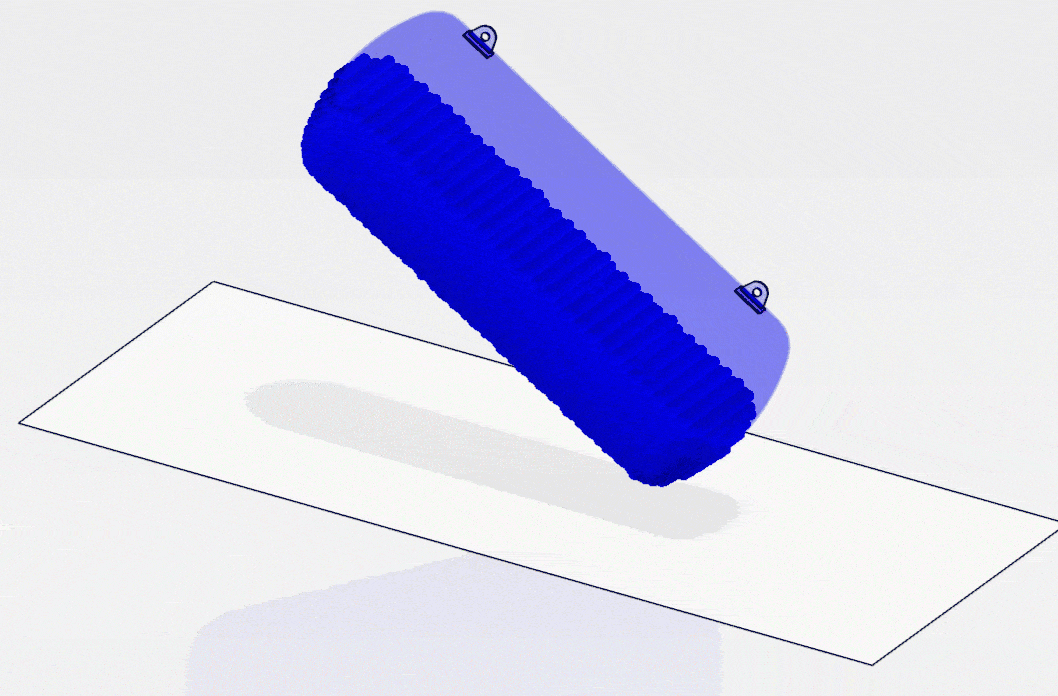
Figure 5
You can see SPH particles as calculated with the explicit solver. The stress profiles of the tank are transparently rendered over the movement of the SPH particles interacting with the solid. SPH particles are perfect for fluid sloshing problems like this, and other cases where the dynamic interaction of the fluid on the structure is important. They are not limited to fluids, though. It can be used in cases like bird impacts on wings, scooping dirt or other debris, and even dynamic interactions like water and clothes in a washing machine! The limitation to SPH elements is that you cannot post-process the fluid properties like turbulence, pressure, etc.
I hope this blog has shown you the incredible power that SIMULIA for SOLIDWORKS brings to the table, coupled with the power of cloud computing it truly is a great tool to help you and your business make better products!
Matt Sherak
Simulation Product Specialist, Application Engineer
Computer Aided Technology, Inc.