SOLIDWORKS TECHNICAL COMMUNICATION: Assembly Motion
For many designers, figuring out how a product will move and interact with other moving parts in a system is integral to the design process. Being able to describe complex assembly motion in the virtual realm is critical to communicate technical information with other designers and customers. From simply demonstrating the way an assembly moves, to specifying a motor or analyzing collision stresses, SOLIDWORKS Motion Studies give us a number of tools to simulate and convey motion.
Motion studies are simulations of motion for assembly and part models (we are going to focus on assemblies in this article). The studies do not change the model directly, but rather use existing mates and assembly conditions in tandem with motion applicators to animate motion in a model. Motion studies can be purely graphical or can analyze physical effects between assembly components such as collision and friction. Results from a motion study can be imported into other SOLIDWORKS applications, such as Visualize for rendering or Simulation for analysis.
There are three types of Motion Studies in SOLIDWORKS: Animation, Basic Motion, and Motion Analysis (Note: Animations and Basic Motion are available in all versions of SOLIDWORKS, but you will need Premium or Sim Pro to run Motion Analyses). In this article, we will look at all three types and discuss why each one might be a good fit for the different types of information you want to communicate. Each type of study is created using the SOLIDWORKS MotionManager, so before we get into the types, we’ll take a look at this often-hidden module in the SOLIDWORKS user interface.
The SOLIDWORKS MotionManager
The MotionManager is a timeline-based interface that we use to set up and execute motion studies. You might have noticed a tab at the bottom of the SOLIDWORKS UI in the “Document Window” area called Motion Study 1 in an assembly you’ve been working on recently.
Clicking this tab activates the MotionManager interface (see the image below). Here, you will see a tree with all the components in the assembly as well as a timeline. The timeline allows you to set a “key point” for each component, or a prescribed position for that component at a given instant in time. Directly above the timeline is a set of playback tools, a button to export the motion study as a *.avi file, and a section for adding motors, springs, and other motion components for more complex studies. Using the MotionManager, you can also set up lights and cameras for the study or use the existing SOLIDWORKS lights and cameras. Finally, the top left corner of the MotionManager allows you to choose what type of study you want to run.
And with that out of the way, let’s discuss the study types a bit more!
Animations
Animations are the simplest type of motion study. You can use animations to (big surprise) animate motion in an assembly. Think of animations like click + dragging moving components in the assembly, with the distinction that instead of moving the components yourself, SOLIDWORKS does that work for you.
To add motion in an Animation, you can either specify motors to actuate motion directly on assembly components, or you can drag the components to a predetermined location and set a key at that point in time. SOLIDWORKS automatically interpolates the motion of the components between key points. SOLIDWORKS also includes and Animation Wizard that helps you quickly create several different types of basic animations.
If you need a simple yet effective method for communicating how an assembly moves, you’ll want to use an Animation. Even if your assembly doesn’t have any motion but you want to show off the assembly from multiple camera angles, you can use animations to impress your boss and customers.
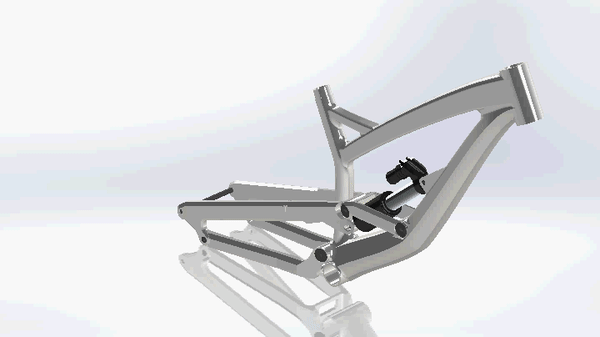
Here’s an example of the downhill mountain bike frame using an Animation.
Basic Assembly Motion
Basic Motion studies take Animations to the next level. Using motion components such as motors, springs and dampers as well as boundary conditions such as friction contacts and gravity, you can create a high-quality animation with real physics behind it. Basic Motion will also account for certain collisions.
Since Basic Motion accounts for material properties like mass and density while calculating motion, it is a bit more time-intensive to set up and run than an Animation. That said, it is ultimately still an approximation.
If you need to create a presentation-level animation that takes simple physical effects like mass and collision into account, use a Basic Motion study.
This Basic Motion study shows the bike hitting a bump. The shock is set up with a spring that damps the impact and rebounds from the bump.
Motion Analysis (SOLIDWORKS Premium or Simulation Professional)
Motion Analysis is a high-accuracy simulation of motion. Just like with Basic Motion, you set up the study using forces, springs and dampers. However, Motion Analysis uses a more sophisticated solver to calculate motion and generates more realistic results. In addition to material properties, inertial effects are considered and calculated. This allows you to generate plots of motion and export collision results to SOLIDWORKS Simulation for further analysis. Motion Analysis results can also be exported to ADAMS software.
There are two types of Motion Analysis: Kinematic and dynamic. Kinematic analyses evaluate the assembly under the influence of motion components, and will help you figure out part displacements, velocities, and accelerations. Dynamic analyses examine the forces generated by the movement and/or collisions. Both types can use either time-based motion (where external actions occur at predetermined times outside of the assembly) or event-based motion (the assembly’s motion triggers external actions).
Since the Motion Analysis solver is more robust than the Basic Motion solver, it takes more time to calculate results. Thankfully, you can use the same setup you used for the Basic Motion study as a baseline for the Motion Analysis study, allowing you to save some computing time by starting off with Basic Motion.
If you want to communicate complex, precise physical information, or if you need to spec a motor/spring or accurately check for interference, your best bet is a Motion Analysis study.
I didn’t set up a Motion Analysis of the bike for this article, but look for a full article down the trail.
*Waving motion*,
Aarya Engineer
Application Engineer
CATI Bellevue