“Under the hood” of SOLIDWORKS Flow Simulation
In Part 1 of this two-part blog I highlighted some of the main characteristics of SmartCells, the unique technology found ‘under the hood’ of SOLDWORKS Flow Simulation that provides for speed, accuracy and ease-of-use of the software. To recap, the five most important features are:
- SmartCells are Cartesian based meshes that are typically an order of magnitude smaller in size (i.e. cell count) than traditional CFD meshes while still providing the same level of resolution and accuracy
- SmartCells handle complex geometries which may have many interfaces between fluid and solid all within one mesh cell
- SmartCells have embedded intelligence which it is uses to speed up the solution process
- SmartCells can handle turbulent boundary layers accurately in all fluid flows
- The combination of easier pre-processing, smaller meshes and quicker run times leads to a significant increase in productivity, making use of CFD within the capabilities of design engineers
In part 1 I covered features 1 and 2 in detail. Now I’ll cover features 3 through 5.
3. SmartCells have embedded intelligence which it is uses to speed up the solution process
The developers of SOLIDWORKS Flow Simulation have devised some unique engineering techniques that can be applied to SmartCell control volumes in order to accurately calculate flow phenomenon such as boundary layers, thin walls and thin channels, even if there is insufficient grid resolution to resolve these phenomena by direct numerical modeling.
One example of this is the modeling of fluid flow in thin slots or channels. Because SOLIDWORKS Flow Simulation maintains a direct link to the native CAD data, the SOLIDWORKS Flow Simulation technology platform recognizes that flow can form in pipes or thin channels. In such cases, analytical or empirical data is used to replace the 3D Navier-Stokes equations with minimal loss of accuracy.
A similar approach is used to successfully model heat transfer in solid thin walls, over thin multilayer structures and within various electronic devices with minimal grid cell counts. The underlying analytical and empirical techniques used in SmartCells have been extensively validated and verified.
4. SmartCells can handle turbulent boundary layers accurately in all fluid flows
Immersed body grids, such as the ones created in SOLIDWORKS Flow Simulation, are generally too coarse for the accurate solution of the Navier-Stokes equations. Resolving the boundary layer accurately with a coarse CFD mesh requires a unique approach. SOLIDWORKS Flow Simulation uses a novel method to solve this problem by coupling the boundary layer calculation with the far field flow:
• A thin boundary layer approach is used when the number of cells across the boundary layer is insufficient for direct calculation of the boundary layer flow gradients
• A thick boundary layer approach is used when the number of cells across the boundary layer is sufficient to accurately resolve the boundary layer
• For intermediate cases, SOLIDWORKS Flow Simulation automatically utilizes a compilation of the two aforementioned approaches, ensuring a smooth transition between the two models
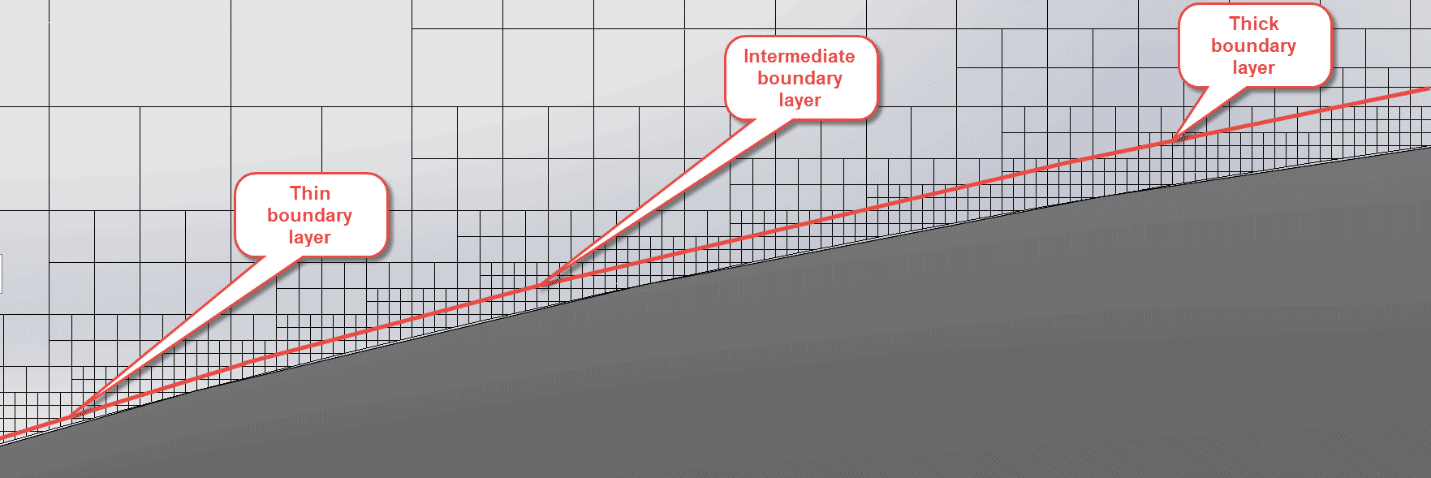
Figure 1: Boundary layer treatment in SOLIDWORKS Flow Simulation
5. The combination of easier pre-processing, smaller meshes and faster run times leads to a significant increase in productivity, making use of CFD within the capabilities of design engineers
SmartCell technology embedded within SOLIDWORKS Flow Simulation has eliminated the tedious and specialized skill of creating highly resolved meshes for CFD and replaced it with a process that is user-friendly, robust and accurate. SmartCell meshes are orders of magnitudes smaller in cell counts than traditional CFD meshes resulting in significantly faster run times and improvements in throughput. Most SOLIDWORKS Flow Simulation runs can be solved in a matter of minutes on standard engineering workstations, eliminating the need for high-end supercomputing hardware. CFD analysis can now be frontloaded to the early stages of the design process, leading to improved product performance across a broad variety of industries and applications. For example, the flow over the submarine that I have used throughout this blog was solved in less than a minute on a Dell laptop, with a total cell count of approximately 20,000 cells.
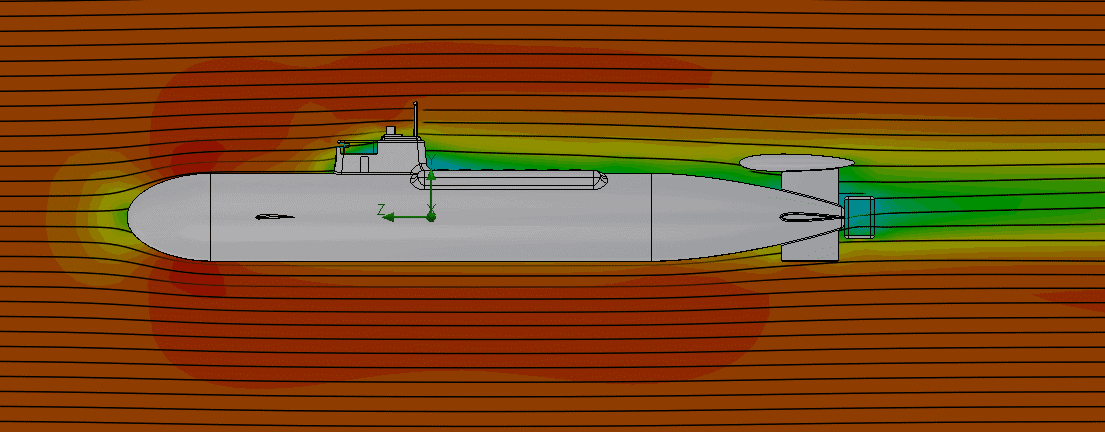
Figure 2: Contours and streamlines of velocity over a submarine
I hope this Blog and its predecessor have piqued your interest in SmartCells, the innovative technology that makes SOLIDWORKS Flow Simulation the powerful, yet extremely easy-to-use CFD package that it is. Now go design some innovative products with the help SOLIDWORKS Flow Simulation!
Alon Finkelstein
Simulation Product Specialist
Computer Aided Technology, Inc.